Engine
& Powertrain Development
CONCEPT & DESIGN
In FC SOLUTIONS to find the concept we start analyzing problems and finding the working principles. Then we combine working principles into working structures and we select suitable combinations with their variants.
The design workflow takes into account all the requirements coming from the specific application. FC SOLUTIONS is able to carry on the complete design process starting from white paper up to 2D machining drawings.
Different approaches of design are part of our engineers know how. Each sectors have own peculiarities for performance or cost reduction.
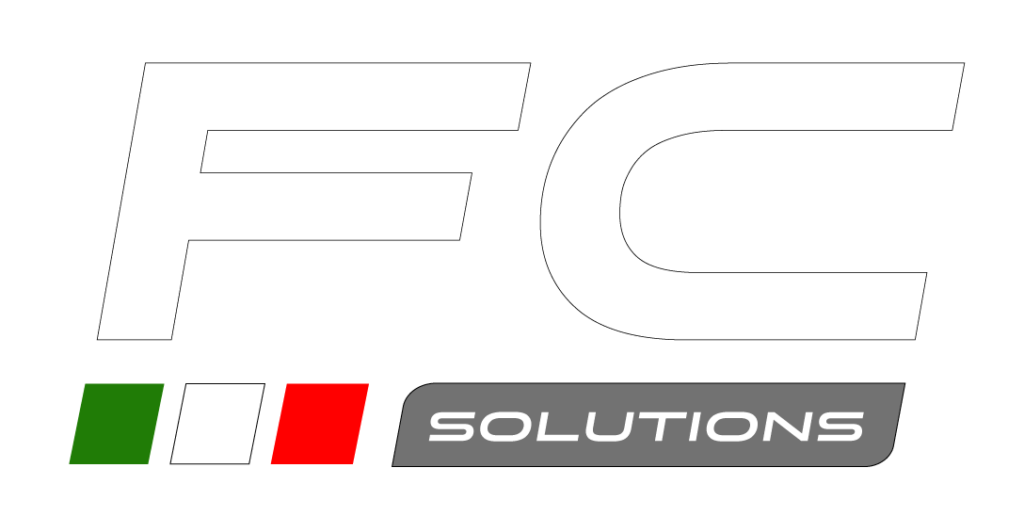
SIMULATIONS
SIMULATIONS
FC SOLUTIONS engineers, cover a wide range of structural, dynamic and fluid dynamic simulations, using of the most popular software and calculation tools. We support the entire design stage, with all simulations necessary to achieve the best solution.
The simulations are made step by step with the design, increasing the accuracy in the last phase of component design.
Providing a simulation approach throughout the product lifecycle, especially at the earlier concept and design stages, can bring to substantial benefits, which ranges from direct cost issues, such as reduced prototyping and shorter time-to-market, to better performing products and higher margins.
It’s possible to divide simulation into three main areas:
- CFD
- FEA
- DYNAMIC
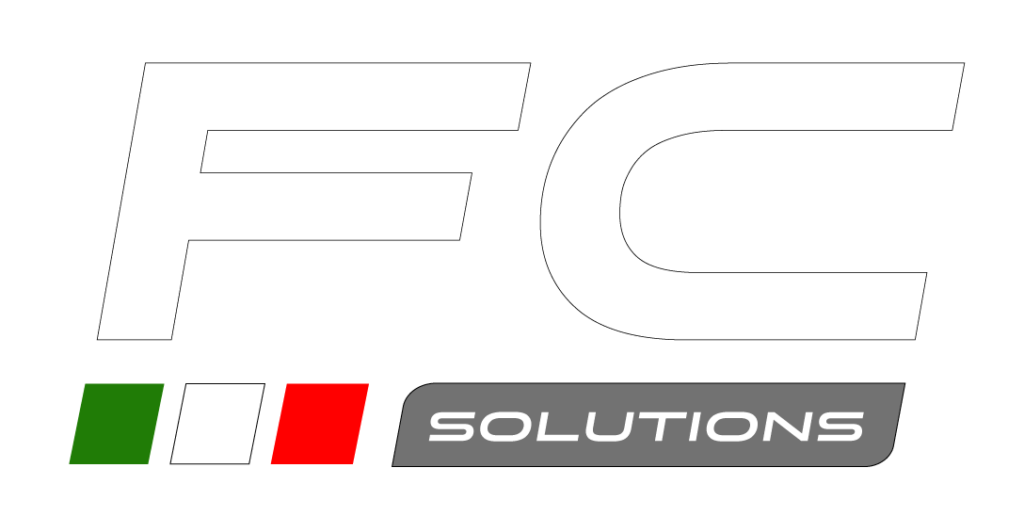
CFD
Computational fluid dynamics is a branch of fluid mechanics that uses numerical analysis and data structures to analyze and solve problems that involve fluid flows. In engine end powertrain development, the FC SOLUTIONS use INTERNAL KNOW HOW in CFD simulations to analyze and optimize of intake and exhaust systems, charge formation process, combustion evolution for each type of engine.
1D CFD use a lumped parameters model for definition and optimization:
-total engine performance and pollutants
-efficiency
-All transient phenomena related to 1D behavior (time to boost in turbo engine)
3D CFD use a 3D CAD model to analyze a virtual component.
- Engine performance
- Intake and exhaust system
- Injection and combustion
- Knock analysis
- Cooling system
- Fluid structure interaction (HTC and Temperature for FEA analysis)
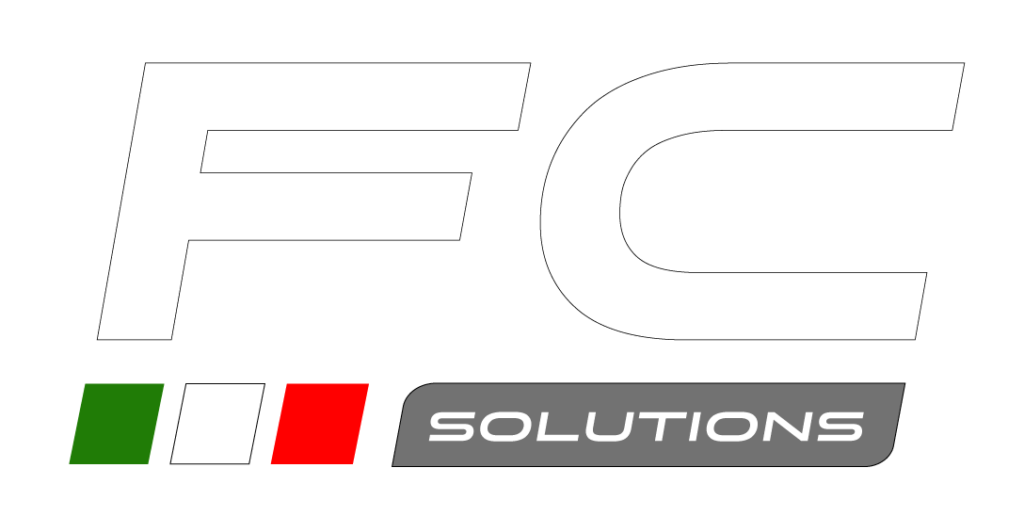
FEA
The Finite Element Anaysis is the use of calculations, models and simulations to predict and understand how an object might behave under various physical condition. FC SOLUTIONS engineers use FEA software to reduce the number of physical prototypes and experiments and optimize components in their design phase to develop better products faster while saving on expenses.
- •Structural strength and component stiffness
- •Linear and non-linear analysis (elastomers)
- •Non-conventional materials analysis (Anisotropy)
- •Fatigue analyses (LCF and HCF analysis)
- •Thermal deformations and thermal structural
- •Modal and harmonic response
- •Shape optimization and mass reduction
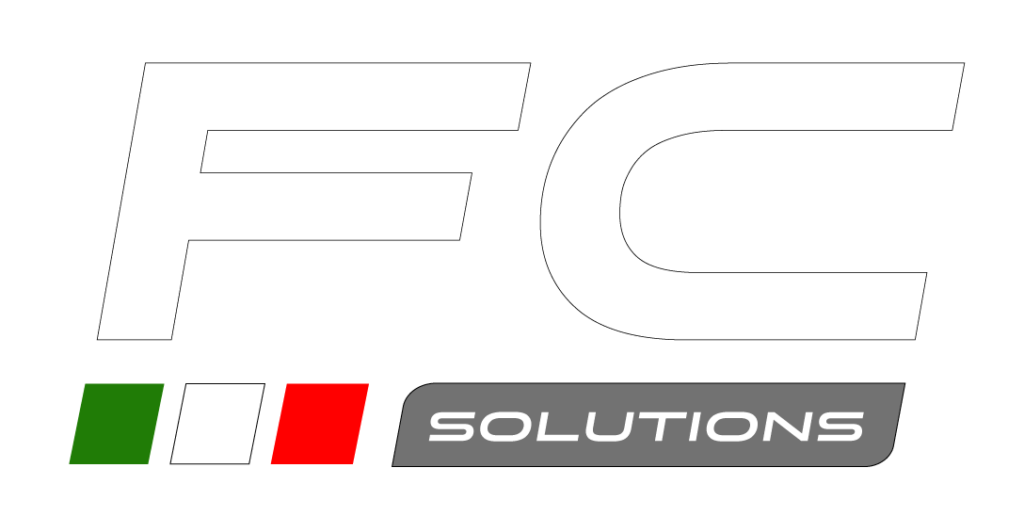
DYNAMIC
Dynamics is the interaction of moving components, considered as flexible bodies, and their structural mechanics, both being investigated using measurement and simulation tools. Multibody analysis becomes particularly relevant when it is necessary to critically evaluate the operating velocities in moving assemblies and the components’ resistance to dynamic loading and it is helpful to predicting loadings generated by the interconnection of components
FC SOLUTIONS use own know how in the following analysis:
- Cranktrain Development (Crankshaft-Conrod-Piston)
- Timing Drive Development (chain or gear drive)
- Complete Valve Train Development
- Complete Powertrain Dynamic Analysis (steady state and transient vibrations)
- Damping and Decoupling Devices (Damper and Pendulum Adsorber)
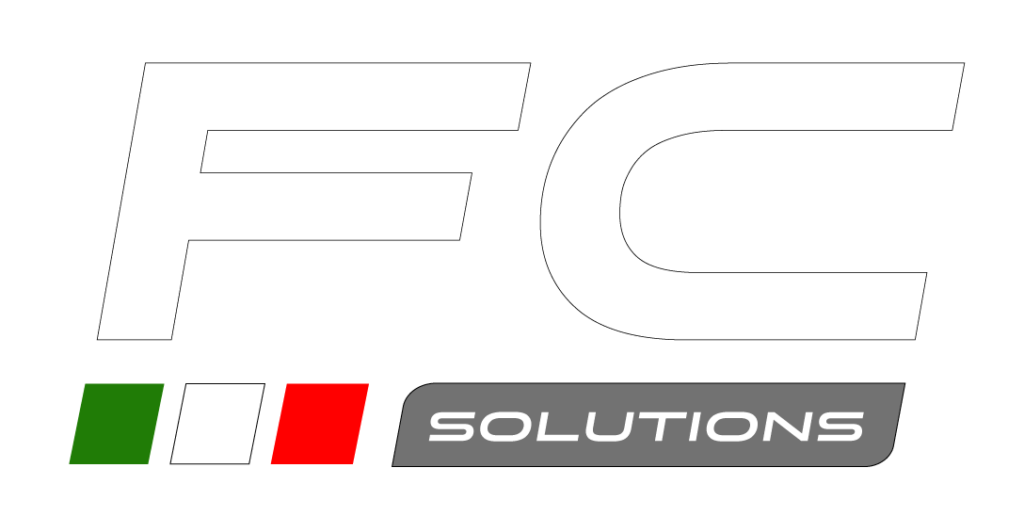
PROTOTYPING
PROTOTYPING
In FC SOLUTIONS we are able to make all component that we design.
In house prototyping division or with our partners we have the resources necessary to produce engine subsistems and other components for automotive, motorsport, aerospace, marine solutions.
Our fully equipped production partners operates to the requirements of these standards with all results fully supported by complete documentation and certification.
Capable of manufacturing quantities from 1 off prototypes to low volume series.
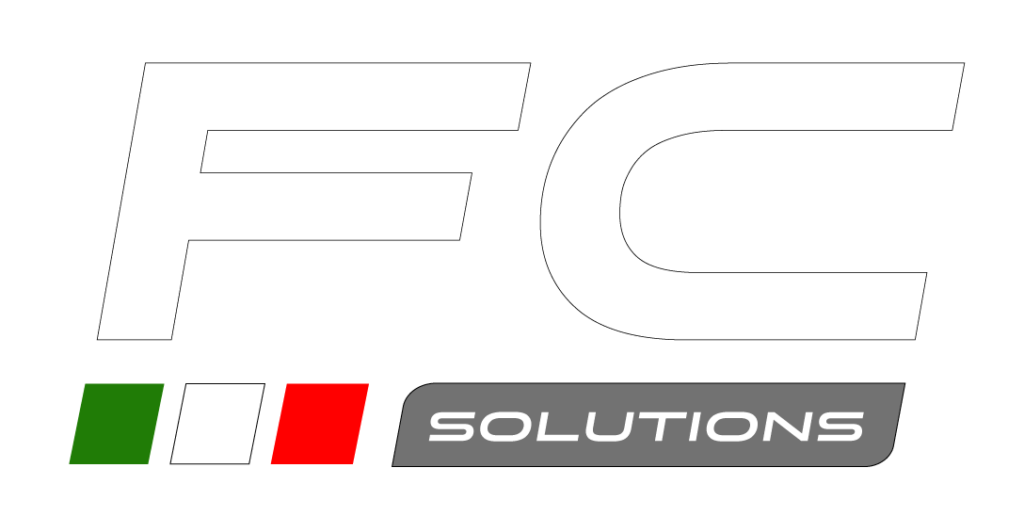
TESTING
TESTING
With support of our partners and University partnership FC SOLUTIONS can perform appropriate component testing
A significant advantage of component testing is its role in reducing the time required to complete the development process.
This reduction in time is due to the possibility of starting the testing without the complete engine/ mechanical system being available.
FC SOLUTIONS can perform a following test:
- Engine Performance and Durability with dyno test rig
- Engine Motored Dyno
- Engine Calibration
- Engine Combustion analysis and optimization
- Valve train test on motoring engine
- Metallurgy and non-destructive testing
- Vibration test
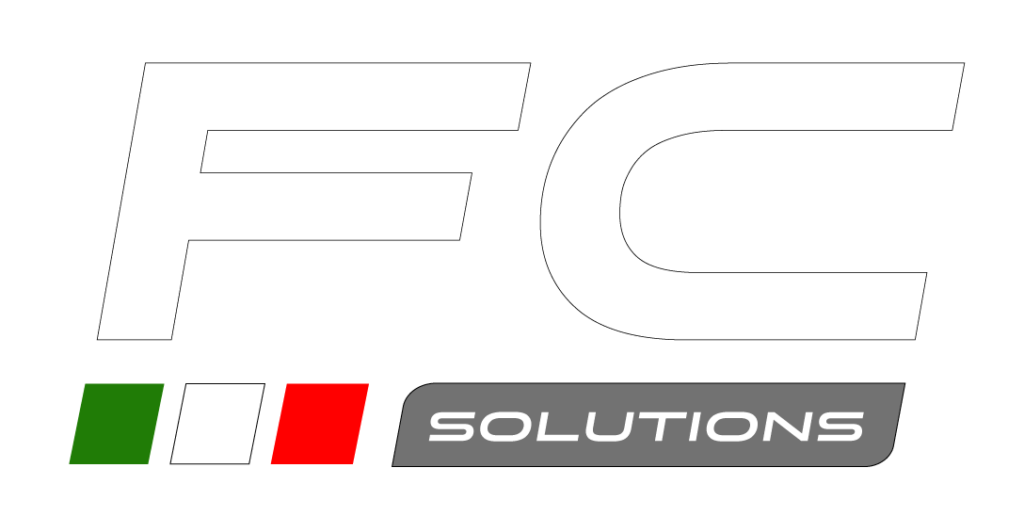
MANUFACTURING
MANIFACTURING
We find the best solution for each problem and will not just settle for a standard approach. Our partners are specialized in machining metals such as stainless steel, titanium, Inconel, copper, magnesium and light alloys. The use of CNC machines and skilled technicians, make us the perfect partner for high precision products.
In Engine and Powertrain Development, FC SOLUTIONS are able to define the manufact of the principal components such as:
- Crankshaft
- Conrod
- Piston
- Cylinder Head
- Crankcase
- Timing sprocket
- Camshaft
- Flywheel
- Clutch
- Drive shaft
- Wheel hub
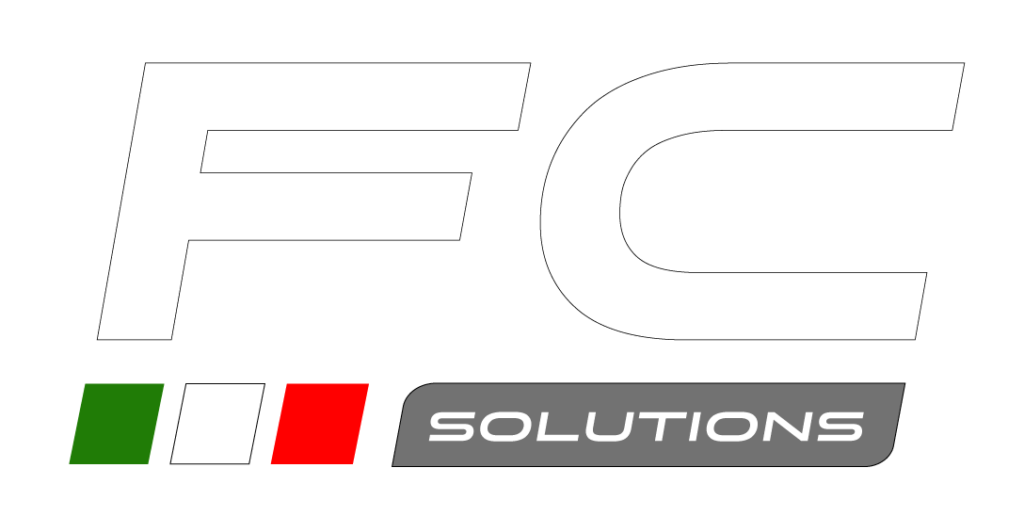
FC Solutions
FC SOLUTIONS engineers, cover a wide range of services. We support the entire design stage, with all simulations necessary to achieve the best solution.
Mon – Fry 8:00 – 17:30,
Sunday – CLOSED
Contacts
-
Via Colle Innamorati, 275
Pescara Cap 65125 ITALY - (+39) 329 061 0426
- info@fcsengineering.it